“…we were able to reduce the asphalt section by 1 to 3 inches and saved another million dollars over and above the savings already realized by FDR.”
Dave Sullivan, P.E., Lumos and Associates, Reno, Nevada
Recently, the Regional Transportation Commission (RTC) in Reno, Nevada, which plans and implements the ground transportation program in Washoe County, completed the rehabilitation of three downtown streets using full-depth reclamation (FDR) with portland cement. Through the use of a Pavement Condition Index system it was discovered that portions of three streets—Mira Loma Drive, Sierra Street, and Hunter Lake Drive—were experiencing base failures and in need of immediate repair.

Sierra Street after reconstruction using FDR with cement.
Issues considered while determining which rehabilitation strategy would work best included project-specific limitations such as the maintaining of curb lip elevations, the presence of cobbles in the subgrade, insufficient or contaminated base, and shallow utilities. The urban setting of these streets and their associated high traffic volumes only added to the challenge. In addition, a limited budget required that the solution be one that minimized construction costs while meeting pavement structural requirements.
Lumos and Associates, a multi-disciplinary consulting firm located in Reno, served as both the engineer and construction manager on these projects. After it was determined which structural section would be required to support projected traffic loading, rehabilitation options were evaluated, including full removal and replacement, partial removal and replacement incorporating geotextiles, thick hot-mix asphalt (HMA) layers, and FDR using cement. Full-depth reclamation proved to be the winner, meeting structural criteria for the roadways while also saving time, money, and reducing construction traffic.
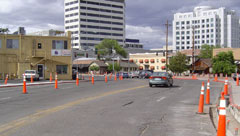
Sierra Street prior to reconstruction
Project designer Greg Lyman said, “Had we gone with a full remove and replace option, we would have spent $4.5 million (15 percent more) than the $3.9 million cost, even when utilizing synthetic reinforcement.” After applying some value engineering concepts such as future maintenance costs and life span for the roadways, Lyman added, “When you look at the costs per square foot for just the roadway structural sections of the projects, the savings are even more dramatic with FDR saving more than 50 percent over the full removal and replacement alternative."
A simple design process was followed that involved digging test pits to obtain representative samples of surface, base, and subgrade materials from the roadways; pulverizing the hot-mix asphalt in the lab; blending the HMA, base, and limited native materials to a representative gradation; adding cement; preparing specimens at optimum moisture and maximum dry density using the modified Proctor test; and testing them for unconfined compressive strength. Four specimens each were prepared at 2, 4, and 6 percent cement and were tested for strength after two, seven, and 28 days. The emphasis on early strength of these specimens was due to the urban nature of the project and the fact that the roadways had to be paved and open to traffic as soon as possible. A cement content of 3.5 percent by dry weight of the pulverized material was found to meet the strength and durability requirements established by the RTC.
The FDR work was performed by Sierra Nevada Construction, Reno, Nevada, and started with the pulverization of the existing roadway to a depth at or slightly below the final bottom of the treatment elevation. Then 5 to 6 inches of pulverized material was removed to ensure that, once the compacted reclaimed/treated base section was completed, the final surfacing course would match existing curb and gutter elevations. Dry cement was spread directly onto the pulverized materials with a cement spreading machine that produced little to no dust. The pulverized, reclaimed material was blended with the cement and, with the addition of water, was brought to optimum moisture. This material was then graded to the appropriate plan lines, grades, and cross-sections, and compacted to a minimum of 95 percent of the established modified Proctor density.
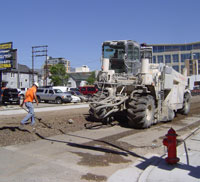
Pulverizing failed flexible pavement in downtown Reno, Nevada
The RTC mandated that all the FDR roadways had to be repaved within seven days due to events planned in the downtown core and to minimize disruption to the traveling public. Because the cement in these roadways was designed to achieve the highest balance between strength and durability, there were some concerns that shrinkage cracking might occur that could reflect back up through the newly placed hot-mix asphalt surfacing. In order to minimize the potential for any reflective cracking of this nature, the roadways were “microcracked.”
Microcracking is the application of several vibratory roller passes to a cement-stabilized base after a short curing stage to create a fine network of cracks. This fine cracking is intended to prevent wider, more severe cracks from forming. Each section of roadway was pulverized, blended with cement, shaped, and compacted in one day, and then moisture cured for 48 hours. The microcracking process was performed at the two-day mark on each roadway, and all sections were paved within 12 hours of microcracking. This process allowed the roadways to be back under traffic in half the time required by the RTC—an added bonus in an urban area.
The stiff, durable cement-treated FDR base layer provided such a stable deck that it allowed the expensive HMA thicknesses to be reduced by 1 to 3 inches, decreasing asphalt quantities by as much as 30 percent. Lyman says the projects went smoothly, and full-depth reclamation cut construction time from eight weeks to six weeks. Reduced construction time allowed for quicker back-to-normal traffic loads and less traffic congestion due to construction barriers. Environmentally, FDR with cement also cut down on the amount of virgin natural resources needed and the amount of hauling and fuel used on the projects.